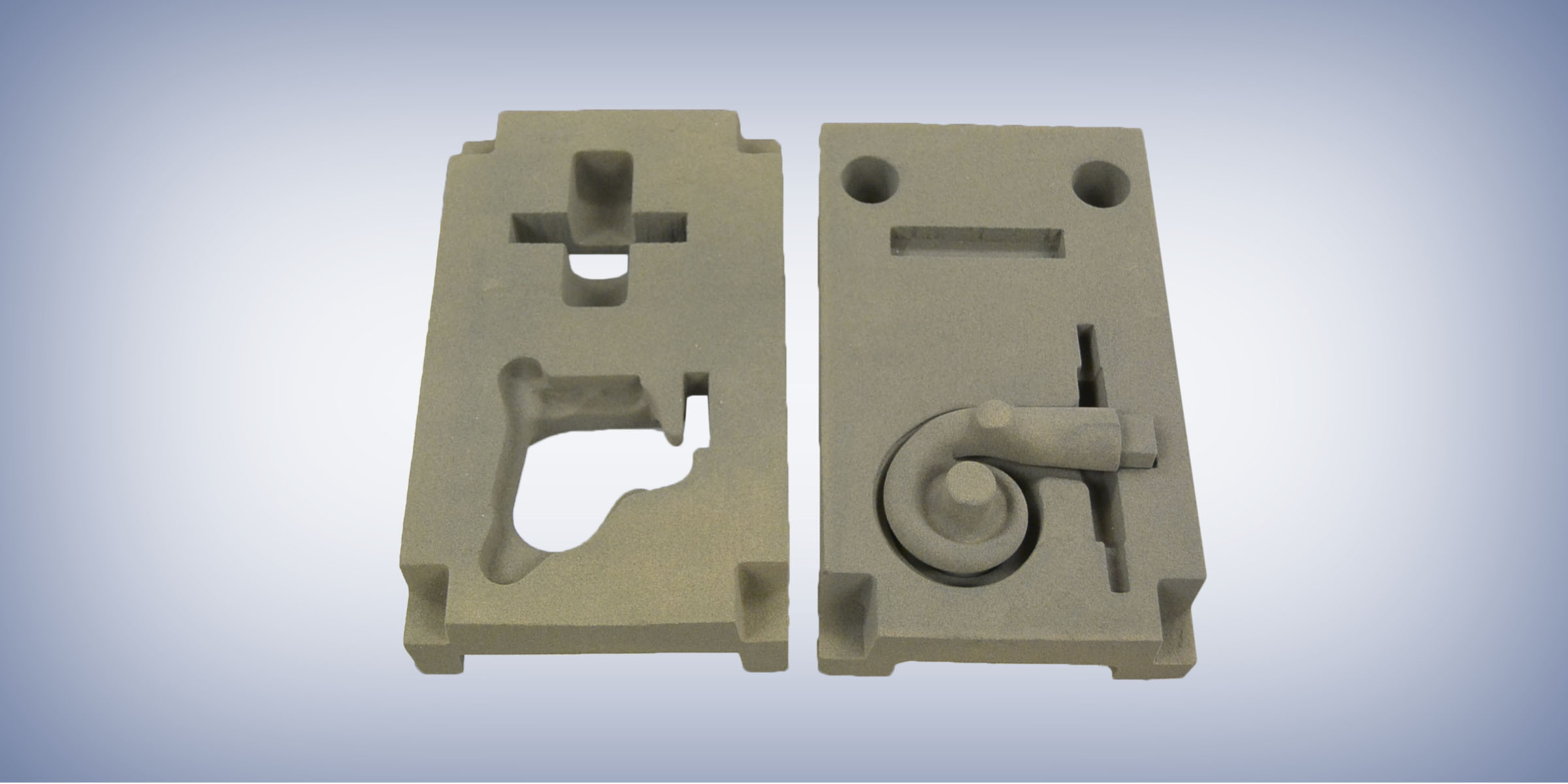
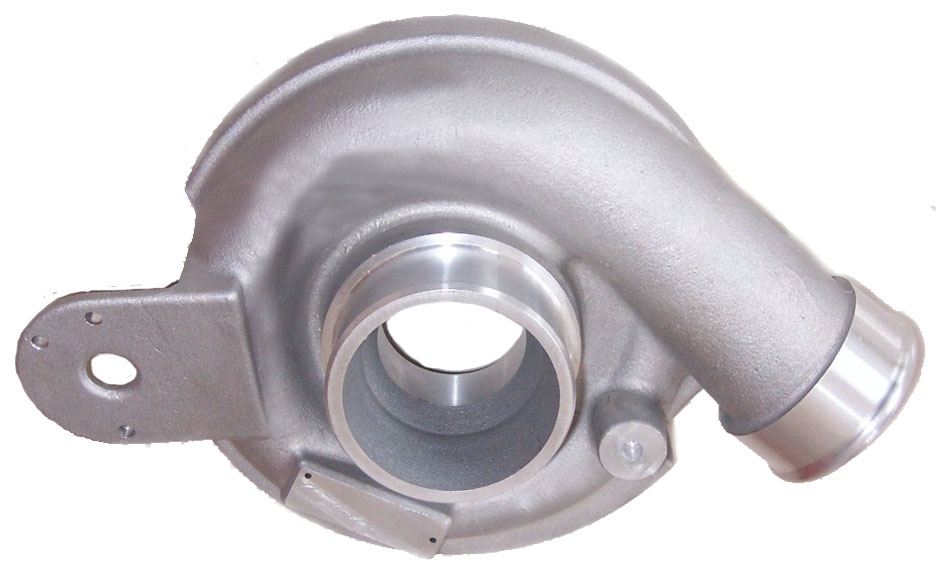
Traditional sand casting usually packs sand around a pattern, or matchplate, to make a mold. With 3D-printed sand molds, a physical pattern is not needed. Once the sand model emerges from the 3D printer, it’s ready to be filled with molten metal. The mold is then destroyed to reveal the new part.
Design Benefits of 3D Sand Casting Services
When you use 3D-printed sand, you get some design benefits that make this process more appropriate than the traditional method. 3D printers work from 3D files, so we can include more intricate details in the mold. This means that, compared to traditional sand molds, printed molds allow for more complex designs.
If you require especially precise tooling, 3D sand casting is a good option to achieve a higher level of detail. In addition to more complex designs, we can execute this technique at a much quicker rate.
Speed Benefits of 3D Sand Casting Services
When we use the traditional method, our team must spend time crafting the wood pattern for the sand mold, and completion can take up to six weeks. With 3D sand printing, the time required for this step significantly reduces. We can produce 3D sand molds within one week. Our 3D printers are capable of fast and efficient output, so we can deliver quality results quickly.
If you have designs you need to execute in a short timeframe, this digital option offers the best choice. We’ll work with you to perfect the design drawings, and then, we’ll execute the sand molds as efficiently as possible.
With both design and speed benefits, there are many reasons to consider 3D printed sand molds in place of traditional patterns. However, this technique may not work for every situation. We can discuss the specs of your project and help you determine the best method to use. Contact us to learn more about your options.