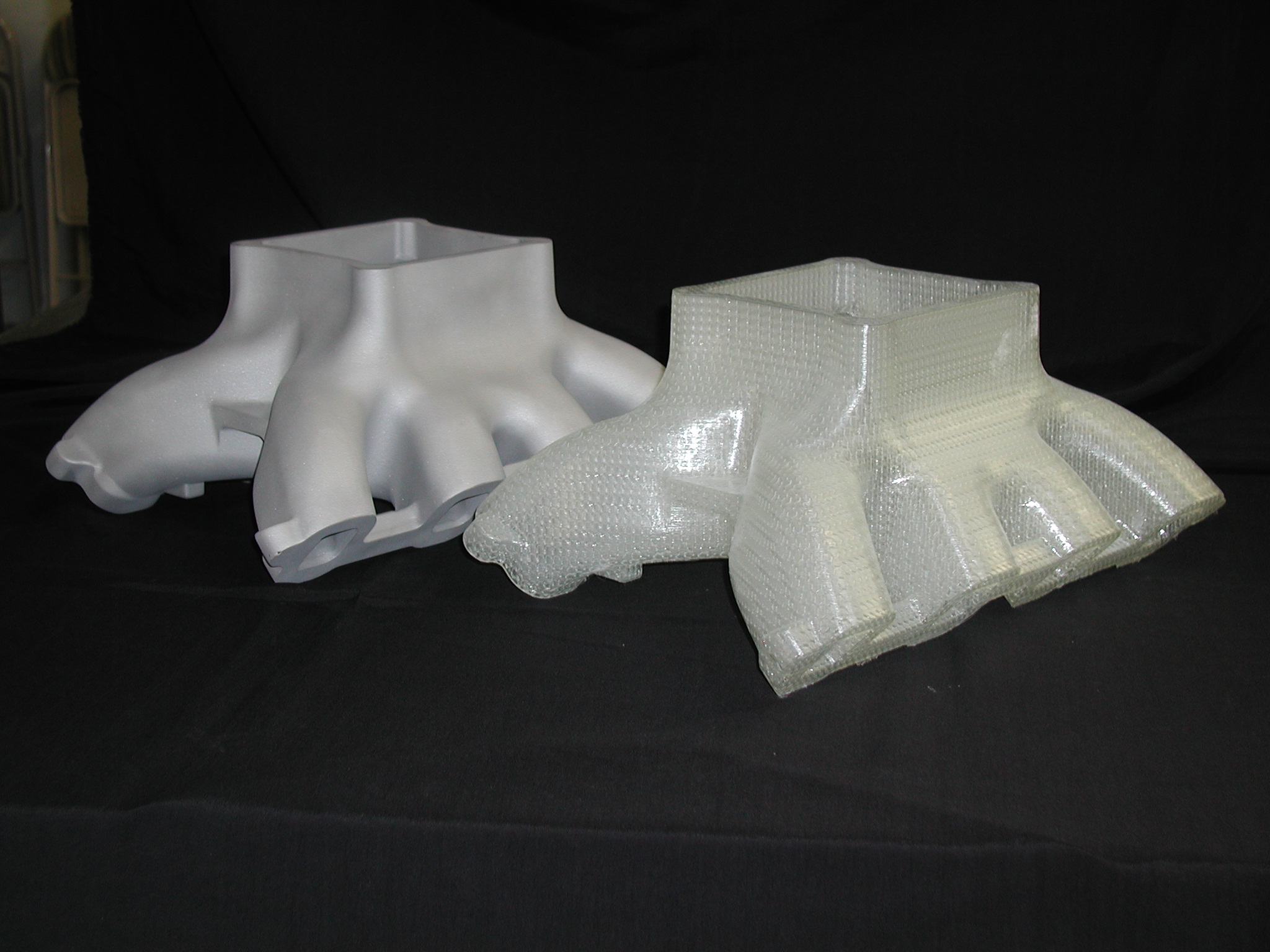
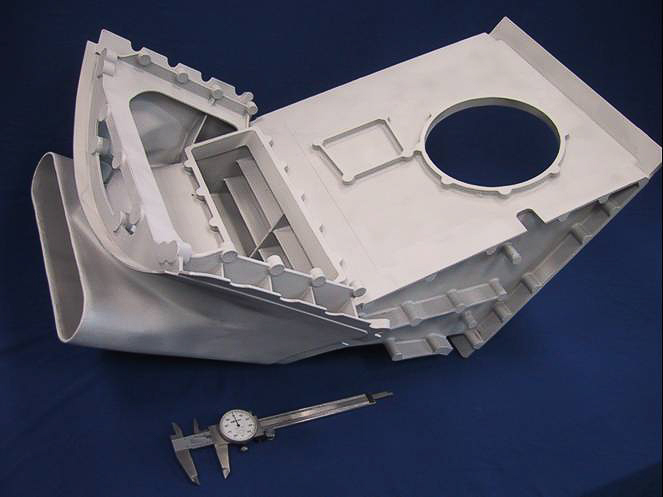
If you decide that lost-wax casting is the appropriate choice for your manufacturing needs, we can deliver fast, efficient service with our 3D printing investment casting services. Incorporating 3D printing into this process has many benefits over its traditional counterpart. We maximize these benefits to produce metal parts that fit and function better. When your parts work better, your entire operation does too.
3D Printed Investment Casting Patterns
Traditional wax casting uses a wax pattern that is tooled, and then invested into (surrounded by) ceramic that forms a mold around the pattern. With 3D-printed patterns, no tooling is necessary. The patterns are burned out just like wax, leaving the ceramic mold ready for metal to be poured into it. Once the metal has cooled, the mold is broken away, revealing the new part. Printing the patterns speeds up the process greatly. The molds can be ready for metal casting within days of receiving the 3D CAD Data.
3D Printing Investment Casting Cost Benefits
In addition to this process’s many benefits, 3D-printed wax patterns help cut down on overall costs. By eliminating the tooling step, fewer expenses become involved. A faster pattern process also enables you to secure your metal parts faster, so you can keep production moving forward.
Ultimately, 3D printing makes a significant difference on the investment casting process. With this technology, we can create very complex patterns, even ones that would be impossible with other methods. Even though parts can be very complex, they will still have exceptional surface quality and accuracy. The 3D printed parts are also more cost effective than tooling a wax pattern. When put together, it’s easy to see why 3D printing investment casting provides the ideal solution.
At FastCastings Inc., we approach each casting project with care and precision. Our expertise allows us to recommend the most efficient and effective process for each unique customer. Contact us today to get a quote for our investment casting services.