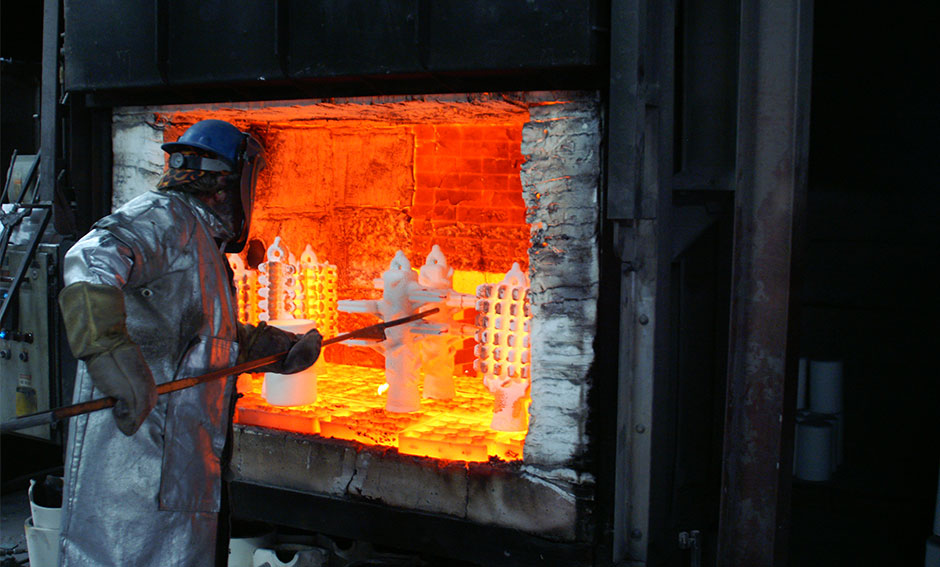
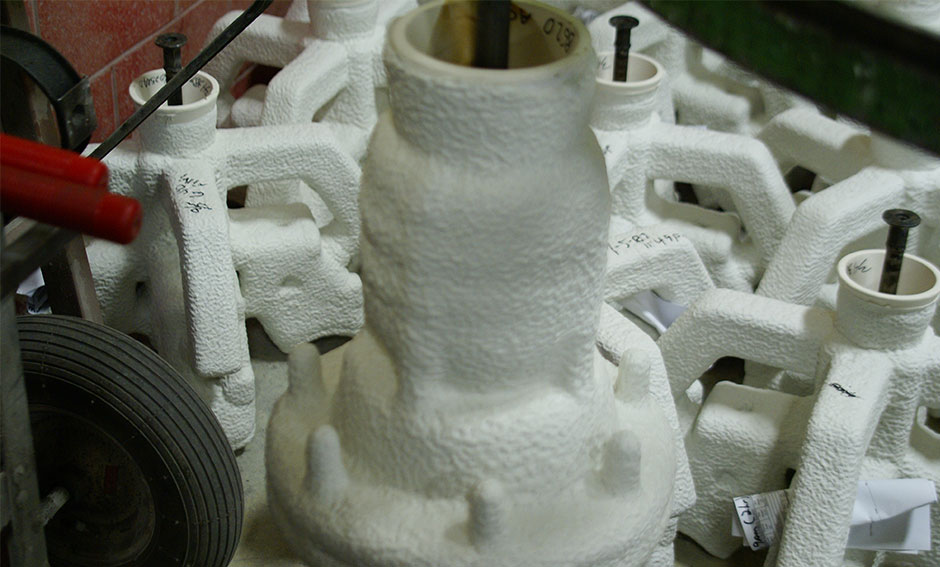
We perfected the investment mold casting process. Here, you can discover what to expect when you choose this option for your project.
Investment Casting Steps
Investment casting is one of the oldest casting processes. Unlike sand casting, this method uses wax to create the pattern. At FastCastings, we use a step-by-step process to complete an investment casting project.
Step One: Create the Pattern
Using design drawings or 3D files, we design and mold the tooling virtually in the computer with super effective simulation software.
Step Two: Create the Mold
Once we have the tooling created via machining, we produce the waxes from the tooling. These waxes are cocooned with a series of slurry and ceramic that hardens to create a mold. Once heated, the wax melts away and leaves a cavity that is an exact duplicate of the desired part. Since the wax is lost, this process is sometimes called lost-wax casting.
Step Three: Pour the Metal
Molten metal is poured into the cavity and left to cool. Once cooled, the ceramic is broken away to reveal the new part. At this stage, we can also complete any finishing work needed with our CNC machining technology as an optional secondary service.
Benefits of the Investment Mold Casting Process
The benefits of investment casting include greater accuracy and higher quality surface finishes. We typically use 3D wax prints for our patterns, so we can use CAD software to capture complex designs and meticulous details. This precise execution results in a better fit for small, intricate parts.
Wax patterns also create a smoother surface for the mold to adhere to, which positively impacts the finish quality. A quality wax pattern sets the standard for each subsequent stage, so the end product is the best it can be.
Now that you know more about our investment mold casting process, you can decide if this option is the right one for you. Contact us if you have any other questions, and we’ll be happy to help!