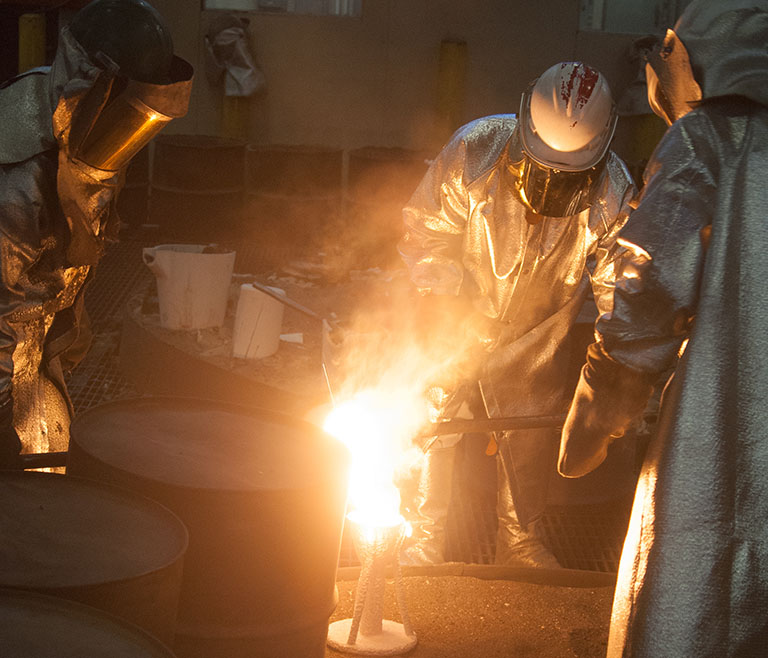
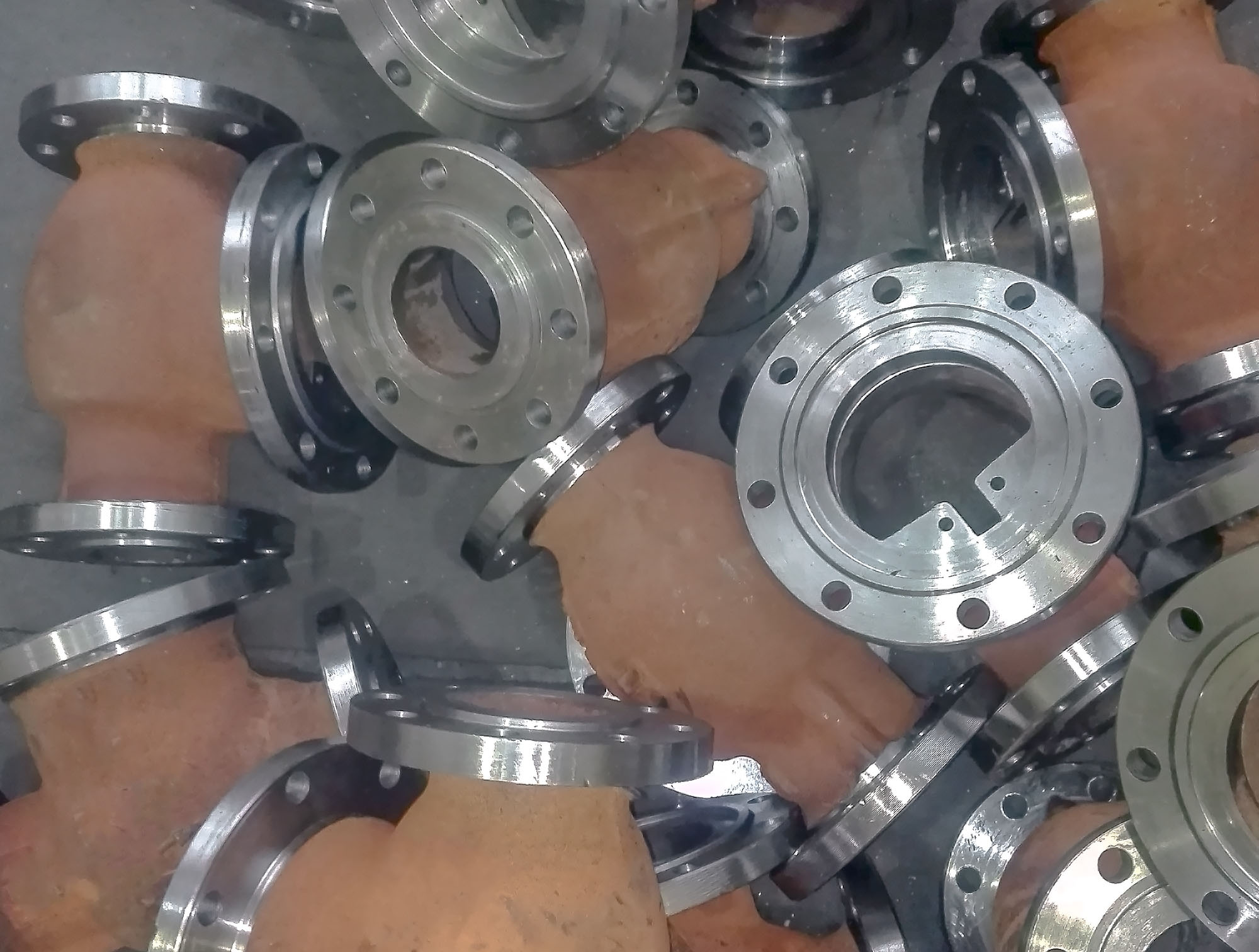
Sand casting is the most widely used casting process. It involves packing sand around a pattern, or model, to form a mold, filling the mold with molten metal, and then destroying the sand to reveal the new part. Since sand can be shaken out of the part, it can be formed into somewhat intricate geometries.
How Do Traditional Sand Casting Services Differ from Digital?
In the traditional method, designers start by drafting the proposed design on paper. Once the design has been finalized, our expert manufacturing team crafts a wood pattern to use for the sand mold casting process. We pack sand around this pattern to create the mold, and now it’s ready for metal casting. When the process is complete, we break the sand away to reveal the finished product.
The process can take up to six weeks from design to completion. This traditional sand casting method provides effective results, and our team consists of expert craftsmen and metal workers. When you choose this service, we guarantee meticulous, quality work.
When Should You Upgrade to Digital, or 3D Printed Mold Casting?
Sometimes, the traditional process isn’t the best option for your operation. If you have many different designs you need to execute, or you have an urgent timetable, our digital option may be more beneficial. In this method, molds are 3D printed. This significantly speeds up the process that traditional tooled processes take. Instead of the expected six-week timeframe, we can have molds ready for casting within days.
If you don’t know which option will work the best for you, let us know! Our qualified experts can evaluate your project and recommend the best process for your needs.
Regardless of which sand mold casting option you choose, FastCastings Inc. is here to help. Contact us to get a quote for our traditional sand casting services.